Testing
Testing of the vehicle will be rigorous and thorough and address three main facets of the vehicles performance. These will be maximum speed, maximum acceleration, differential housing deflection and maximum temperature produced. The maximum achievable speed can be tested by measuring how much distance is covered in a given amount of time on a flat smooth surface. The maximum achievable acceleration can be tested by measuring how much time elapses between the vehicle starting from a stop, and reaching its maximum achievable speed on a flat smooth surface. The maximum temperature produced by the drivetrain can be measured by running the vehicle at maximum speed for a given amount of time, and measuring the temperature of the motor using a thermistor tipped thermometer in a room at room temperature. The diff housing deflection test was carried out by adhering a high precision machinist ruler to the diff housing, propping up the rear end, then running the vehicle at maximum power. The average deflection along the top plane of the housing was measured this way.


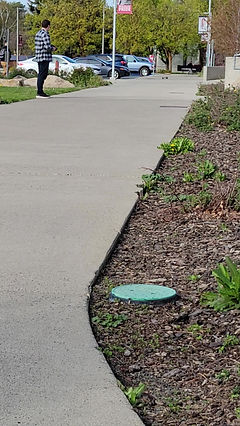
Figure 1: Shock towers removed for diff housing deflection test
Figure 2: Using a temp gun to measure the temperature of the drivetrain components during the temperature test.
Figure 3: One of the maximum speed test trials. A phone with a speedometer app enabled was secured under the body of the vehicle. This app would log the maximum speed achieved after it had been initiated.

Figure 4: A screenshot from the speedometer app that was used during the maximum speed test. As can be see, the maximum speed achieved during this trial was 20 mph.

Figure 5: The competition drag race in which some speed data was collected
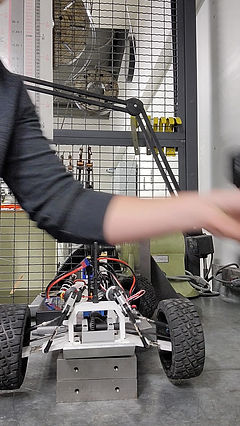
Figure 6: A short clip from the temperature test being performed.
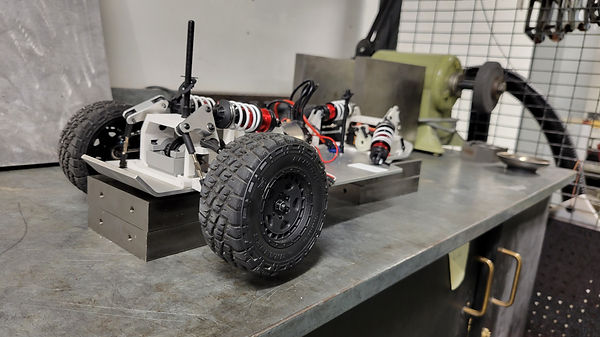